A Comprehensive Guide to Carrying Out Foam Control Solutions in Your Workflow
Reliable foam control is a vital element of functional efficiency that commonly goes neglected. Recognizing the details of foam generation can considerably influence both productivity and product top quality. This overview lays out the numerous difficulties postured by foam and the varied solutions offered, providing a framework for choose and implementing one of the most appropriate approaches. By examining key elements such as application compatibility and personnel training, companies can optimize their foam administration initiatives. As we discover these components, the capacity for transformative enhancements in your operations comes to be obvious. What steps will you take following?
Understanding Foam Obstacles
Foam difficulties are a considerable problem across numerous markets, impacting functional performance and item quality. The formation of extreme foam can prevent procedures such as mixing, transport, and storage space, leading to boosted downtime and waste. In industries like food and beverage, pharmaceuticals, and petrochemicals, foam can disrupt manufacturing lines, triggering item variances and contamination threats.
Furthermore, foam can obstruct devices capability, leading to pricey repairs and upkeep. As an example, in wastewater therapy, foam can disrupt clarifier operations, causing reduced therapy efficiency and governing compliance concerns.
Understanding the underlying root causes of foam generation is vital for reliable management. Elements such as surfactants, temperature changes, and frustration levels can all add to foam manufacturing. Determining these aspects enables industries to implement targeted approaches that minimize foam formation while maintaining product honesty.
Sorts Of Foam Control Solutions
Mechanical options include the usage of gadgets such as foam skimmers or defoamers. Chemical remedies, on the other hand, include the application of defoaming representatives-- compounds that interfere with the foam framework, leading to its collapse. Foam Control.
Lastly, operational techniques concentrate on process adjustments. This might involve changing equipment specifications, such as temperature and stress, or altering the flow rates of fluids to minimize foam generation. In addition, executing good housekeeping techniques can also mitigate foam development by reducing impurities that contribute to foam stability.
Choosing the ideal foam control service entails evaluating the certain requirements of the operation, including the sort of procedure, the attributes of the products entailed, and safety and security factors to consider.
Picking the Right Products
Choosing the right foam control products requires an extensive understanding of the specific application and its unique obstacles. Variables such as the kind of foam, the atmosphere in which it occurs, and the wanted result all play pivotal functions in item selection. Foam Control. In sectors such as food processing, it is critical to choose food-grade important link defoamers that abide with safety and security regulations while successfully taking care of foam.
Furthermore, take into consideration the viscosity of the liquid where the foam problem exists. Some items are created for low-viscosity applications, while others are customized for thicker fluids. Compatibility with existing processes is an additional essential aspect; the chosen foam control agents need to integrate effortlessly without interrupting general procedures.
An additional vital variable is the technique of application. Some items might need dilution, while others can be used directly. Analyzing the convenience of usage and the needed dose can offer understandings into the item's efficiency and cost-effectiveness.
Implementation Techniques
Successful execution methods for foam control remedies call for an organized approach that lines up item option with functional demands. The initial step includes a thorough evaluation of the procedures where foam takes place, identifying specific areas that require treatment. By involving cross-functional groups, including design, production, and top quality guarantee, organizations can gather insights that educate the choice of one of the most efficient foam control items.
Next, it is essential to establish clear purposes for foam decrease, ensuring that these goals are quantifiable and achievable. This might entail defining acceptable foam degrees and the timelines for application. Educating personnel on the buildings and application techniques of chosen foam control representatives is just as important, as correct usage is vital for optimal outcomes.
Additionally, integrating foam control solutions into existing process calls for cautious preparation. Inevitably, a well-structured strategy will certainly enhance operational efficiency while properly taking care of foam-related obstacles.
Surveillance and Evaluating Performance
Surveillance and assessing the effectiveness of foam control remedies is important for ensuring that applied techniques generate the go to this site desired results. This process involves organized information collection and analysis to assess the performance of foam control representatives and strategies. Key efficiency signs (KPIs) must be established before application, enabling a clear standard against which to measure development.
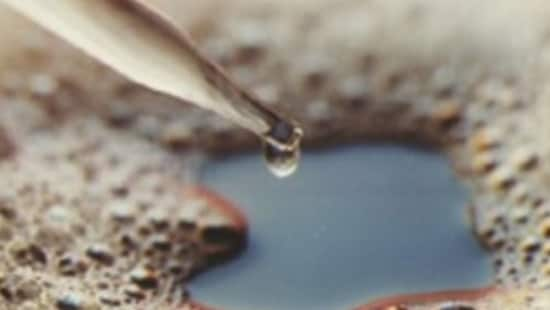
Examining efficiency likewise needs regular evaluations of foam control treatments and representative efficacy. This can be accomplished via sampling and screening, allowing operators to identify if present options are meeting functional requirements. It is essential to solicit feedback from group members who communicate with these systems daily, as their insights can disclose functional subtleties that quantitative data might neglect.
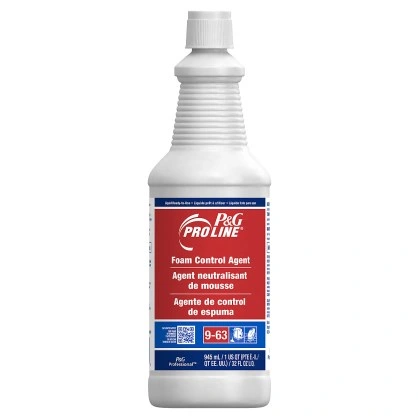
Ultimately, an organized surveillance and assessment framework assists identify essential modifications, ensuring that foam control solutions remain effective, affordable, and aligned with business objectives.
Final Thought
Finally, efficient foam control remedies are necessary for optimizing operational effectiveness and maintaining product high quality. A thorough understanding of foam difficulties, integrated with the choice of suitable items and implementation techniques, assists in the successful monitoring of foam generation. Developing quantifiable KPIs and spending in personnel training even more boost the effectiveness of foam control actions. Normal tracking and assessment ensure continuous renovation, ultimately bring about a more streamlined and effective operational environment.
Applying good housekeeping techniques can additionally reduce foam formation by lowering contaminants that add to foam security.
Choosing the right foam control items calls for a thorough understanding of the specific application and its one-of-a-kind challenges (Foam Control).Effective execution techniques for foam control solutions need an organized strategy that aligns item option with operational needs.In verdict, effective foam control remedies are essential for maximizing functional efficiency and keeping product top quality. A comprehensive understanding of foam challenges, integrated with the selection of suitable products and execution methods, assists in the successful administration of foam generation
Comments on “Innovative Foam Control Solutions to Boost Your Production Processes”